At JPSKILNS, we have to offer more than kilns supplies. Take a look at this article and besides offering you kilns supplies, we are going to give you some information about kilns.
How many types of kilns are there?
Traditionally, kilns were heat chambers built from bricks and fueled by wood or coal. Nowadays, kilns come in many styles and sizes, and they are usually powered by electricity or gas. There are many different types of kilns, many of which are normally used for pottery and the ceramic arts.
However, it is important to note that there are more types of kilns available so that creators may creatively explore other mediums. According to the different materials they work with, kilns are categorized into four categories: lampworking kilns, ceramic or pottery kilns, fusing kilns, and PMC or enameling kilns.
Here we’ll cover everything you need to know about these kilns, so you can make the best choices for your artistic practice and once you know more about kilns supplies and answer your question about what are the different types of kilns.
Lampworking Kilns
Lampworking is a millenary technique that lets artists mold glass to their creativity’s liking. This technique is ideal for smaller-scale creations, such as beads, jewelry, and other art pieces. As a very complex art form, it requires mastery and skills that can only be acquired through practice.
In order to manipulate glass, it must reach very high temperatures. This is where a specialized kiln comes in handy. The kiln is used at the end of the process so the piece at hand may anneal. Annealing refers to heating a piece of glass until its temperature reaches a stress-relief point. This point is reached when the glass is still too hard to bend but is soft enough for its internal stresses to be relieved.
Following this step, the piece must be soaked in heat until its temperature is uniform throughout. Once this happens, the piece must then be cooled at a slow rate so that its internal temperature goes below a critical point and there are no internal stresses. This allows the piece to drop to room temperature safely so that it doesn’t crack or shatter when it later faces minor temperature changes or other shocks.
Lampworking tools
Fully finished lampworking pieces require two types of tools: heating and shaping tools. The main tools for heating glass are a bench burner, a hand torch, and the previously mentioned kiln. The first two allow for the lampworker to bend glass pieces as desired.
The bench burner provides a stable flame that remains still, and the hand torch allows for movement and direction of the flame. The kiln makes sure the temperature changes that the piece goes through are stable enough for it to remain intact until it reaches room temperature and it is ready to be safely used.
In terms of shaping tools, the mandrel is one of the most essential instruments used in lampworking. A mandrel is a stainless-steel rod around which glass is shaped. It is important to use bead-release formula, a mixture that prevents the glass from sticking to the mandrel while it is being wrapped.
Other common shaping tools are paddles, mashers, tweezers, and picks. Several different finishes and styles can be achieved through these tools, and they can be combined for even more creative results.
Other tools in the market include reamers, shears, claw grabbers, and lathes. Reamers are specifically used for bead making since they allow artists to open a space in the middle of the bead, so a string may go through it. Shears are used for cutting molten glass, claw grabbers are for holding hot glass safely, and lathes rotate pieces so that indentations and textures may be added to their surface.
Another common lampworking tool is a marver, a flat piece of material that can be used to shape beads. It is usually made from graphite, which draws heat out of the bead, so this can create interesting effects on special glass that has certain properties. A marver can be torch mounted or handheld, depending on the degree of manipulation required.
Ceramic / Pottery Kilns
Ceramic or pottery pieces need to reach very high temperatures so that the chemical and physical reactions in the clay permanently alter them, turning them into safe and functional items.
Ceramic kilns provide that possibility since modern models are easier to set up, control, and even program. Artists need to be fully aware of the temperature changes their pieces are going through, so having a kiln that can be set to specific temperatures will guarantee that the firing process goes by smoothly.
Electric Ceramic Kilns
Electric kilns are extremely popular due to their simplicity and reliability at a rather accessible price point. This type of kilns supplies will certainly make loading and firing easier for artists and creators. This type of kiln is built as a closed chamber made from soft, porous, and highly insulating bricks.
There are channels that run inside its interior walls where coils made from a special metal alloy will run and act as heating elements. A strong electric current will be sent through these coils for it to cause friction and eventually heat up the whole chamber. The heat produced inside an electric kiln is evenly spread and easily controlled, therefore being a reliable firing method.
Fusing Kilns
Controlling the temperature at which materials are heated is the key to achieving varying levels of fusion when working with glass. Using a specialized kiln to combine glass elements makes sure that the temperature is kept even so that cracking within a piece is prevented.
There are several things to consider before selecting a kiln for glass fusing purposes. The first one involves its shape, which is usually either oval or rectangular. Glass products fired in a rectangular kiln will normally cool faster than those fired in an oval kiln.
JPSKilns offers small glass fusing kilns supplies models, that only emit electric resistance within their interior side panels. The structure of these kilns is composed of a chamber with a floor area, interior walls, and a lid. These elements are all made from high-quality materials and are able to be personalized for better compatibility with your projects. All of these models include a digital programmer so that you are in control of the firing process at all times.
Glass fusing
Glass fusing is a technique where two or more pieces of compatible glass are merged into a single piece. There are degrees to which this method may be applied: two pieces of glass may be made just malleable enough to stick together, or they could also be fully integrated into each other.
To achieve these results, artists must select the proper glass to be fused. Different types of glass have different coefficients of expansion (COE) which refers to the rate at which the material changes in size as the temperature around it changes.
To fuse two or more pieces of glass, it is very important that they are all compatible with each other, which means they share both COE and viscosity levels. Viscosity refers to how much glass starts flowing as it melts. Glass pieces also need to inherently have fusing properties, regular glass won’t do the trick. This special kind of glass that can fuse is also known as dichroic glass.
After choosing the right type of glass, the different pieces that will make up the final product have to be cut and arranged. Then, the pieces are loaded into the kiln so that they can all merge into one single item. Before removing your piece from the kiln, it is very important to let pieces cool off completely.
Precious metal clay (PMC) Kilns
Kilns designed for metal clay are programmable and easy to use. Other mediums such as copper and bronze may also be fired in this kind of kiln. The main factors to consider when selecting a kiln for your PMC projects are kiln size, temperature maximums, interior materials, loading style, technical features, and accessories.
The size of your kiln needs to respond to the type of projects you intend on firing. If you’re planning to do larger pieces, maybe even use it for firing other materials, a larger kiln is recommended. The same goes if you intend to produce pieces in large quantities frequently. If what you plan to do is jewelry or bead making, or if you’re a beginner in the practice a smaller kiln is better for you.
Consider that a kiln´s power is reduced over time, so make sure to overestimate the temperature of your projects by 200-300 degrees Fahrenheit when choosing the correct kiln for your practice.
There are two types of interiors when it comes to metal firing kilns: brick or ceramic fiber. Brick interior kilns take longer to heat but they can endure higher temperatures, while ceramic fiber ones heat up faster, reducing firing times.
Brick interior kilns need to be cleaned more regularly because their heating elements are exposed, while ceramic fiber kilns need to have the interior completely replaced if one of their internalized heating elements exceeds its capacity.
Having a brick interior kiln will assure insulation that makes the temperature stable while having exposed heating elements allows for easy replacement and maintenance of the kiln in question. When selecting the best PMC kiln, make sure to notice the type of controller and if it includes a viewing window. A manual controller requires you to be in control of the temperature changes, while a digital one regulates the temperature and deactivates the kiln when needed. Viewing windows or viewports are recommended if you want to supervise your projects while they’re being fired.
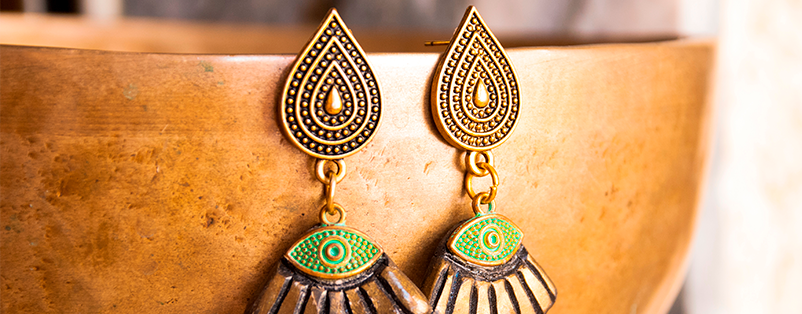
Enameling Kilns
An enameling kiln is a small tabletop kiln used for testing glazes or decorating jewelry, glass, metal, or pottery. Enameling refers to the application of a hard and glossy decorative or protective coating that fuses with its substrate when fired in an enameling kiln.
Adding a tabletop jewelry kiln to your studio is a great option for those looking to explore new finishes and results. Portability, durability, material, temperature limit, and design are just a few of the characteristics that need to be considered before investing in a kiln for the purpose of enameling jewelry.
Having a digital control will certainly give the kiln an advantage since electronic controls allow you to set up specific conditions and times for the project at hand. This way, continuously monitoring the kiln as it fires isn’t required. To choose the appropriate kiln size, you need to consider if it will fit into your workspace and how many jewelry pieces you’re looking to fire at once.
Kilns for sale
When looking to buy a kiln for your artistic practice, JPS Kilns has an extended catalog of first-rate models to choose from. Our kilns supplies are made of a selection of forty different kilns provides a wide variety of options that can cater to all sorts of requirements and needs.
There are currently 16 lampworking kilns, 18 ceramic/pottery kilns, 4 fusing kilns, and 2 PMC/enameling kilns available for purchase at the JPS Kilns shop. Our kilns are made from high-quality materials, and providing reliability and practicality, these kilns will bring your ideas to life with no issues during your process.